CATIA V5 COURSE CONTENTS
1. Introduction:
A. Basic Applications of software.
B. Environment of CATIA.
C. Specification Tree.
D. Applying Material to Part.
2. Sketcher Workbench:
A. Creating objects by using Profile Toolbar.
B. Sketch Tool, Standard-Construction Elements.
C. Editing with Operation Toolbar.
D. Applying Constraints and changing constraints.
E. Sketch Analysis and Diagnosis.
3. Part Design Workbench:
A. Creating Sketch based feature: Pad, Shaft.
B. Addition of features and Pocket, Groove Features.
C. Reference Elements- Point, Line, Plane.
D. Limiting Elements and Advance option.
E. Hole, Stiffener, Solid combine feature.
F. Dress-up Features- Fillet, Chamfer, Draft, Thickness, and Tap.
G. Advance Features like Rib and Slot.
H. Multi section Solid and Remove Multi Section.
I. Duplication of Features.
J. Define in Workbench options.
K. Measure Elements, area, volume, mass, inertia.
L. Transformation feature, Mirror and Scaling.
M. Rectangular, Circular and User Defined Pattern.
N. Working with Bodies and Boolean Operation.
4. Assembly Workbench:
A. Top down and Bottom up approach of Assembly.
B. Inserting components to Assembly.
C. Changing Properties of component.
D. Manipulation, Snap, Smart move operation.
E. Applying constraints to parts.
F. Sub-assembly in Assembly.
G. Activate/Deactivate component.
H. Checking clearance and interference in Assembly
I. Sectioning Assembly.
J. Create Exploded view of Assembly.
5. Drafting Workbench:
A. Creating views: front, Projection, Section, Auxiliary, Detail, etc.
B. Dimensioning and Auto dimension in drawing.
C. Adding Annotations, Tolerances and symbols.
D. Creating Frame, Title block.
E. Exploded view and balloon in Assembly view.
6. Surface Design:
A. Wire frame and Surface Design
B. Generative Shape Design
C. Wire frame tools like circle, spline, corner, helix
D. Surface Tools: Extrude, Revolve, Sweep, Fill, Multi-section Surface, Blend
E. Methods of trimming surfaces
F. Projection/ Intersection of wire frame and surfaces
G. Joining of surfaces
H. Transformation Toolbar
I. Extract, Boundary, Fillet, Extrapolate
J. Creating Solids from Surfaces
7. Generative Sheet Metal Design:
A. Sheet Metal Parameters: Thickness, Bend Radius
B. Walls and Flanges
C. Bending Option
D. Fold and Unfold of sheet metal part
E. Stamping Option
F. Recognition of sheet metal from solid
Friday, October 10, 2008
Saturday, September 27, 2008
CAD CAM TRAINING
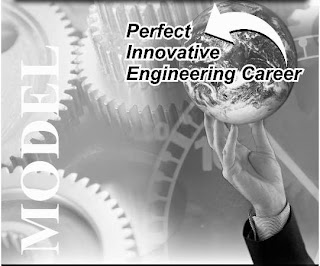
MODELCAM
AutoCAD, CAD-CAM-CAE, CNC Programming
MODELCAM Engineering Technology is leading organization in the field of Training, Design and Development of Mechanical Engineering. We are having more than 5 years of experience in this field. We are working with expertise team of Engineers. We provide training and services in AutoCAD, CAD-CAM-CAE and CNC programming.
We are expert in CAD-CAM software like CATIA V5, UG and Pro/E. We are proud to be provide world class AutoCAD, CATIA training in Nashik. Many of our students have joined MNCs after compeletion of course. We have build leadership for AutoCAD, CATIA in Nashik.
We are expert in CAD-CAM software like CATIA V5, UG and Pro/E. We are proud to be provide world class AutoCAD, CATIA training in Nashik. Many of our students have joined MNCs after compeletion of course. We have build leadership for AutoCAD, CATIA in Nashik.
We provide services like Product Design, Fixture Design, Tool Design, Reverse Engineering, Solid Modeling, Detailing, Isometric Drawings, CAD drafting, Data management-conversion, Plotting and Scanning up to A0 size.
We have provided corporate on site AutoCAD, CATIA Training and Design related services for our esteemed clients like Mahindra, VIP, HAL, Legrand, Ring Plus Aqua, L& T, Reliable, IREEN, Crompton, Mahindra Ugine, Indian Tools, and many industrialist in Nasik.
For More Details You May Contact to
Dinesh Deore
MODELCAM Engineering Technology
1, Liberty Point, Below Sankheda Furniture,
Racca Colony, Sharanpur Road, Nashik - 2
Ph. 0253 - 2582186, 3012586
Mob. 94222 48005
Email: modelcam@gmail.com
Subscribe to:
Posts (Atom)